>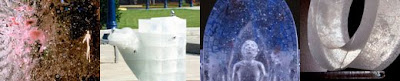
This coming June, Bullseye Glass hosts their glass arts conference in Portland, OR. The biennial conference is a great way to see the latest BE glass products, tour the factory and network with other glass artists and educators. Scholarships are available – read below:
CROSSOVER: A Material Exchange
Exploring the interface between kiln-glass and other media
What can the “makers” in the field of kiln-glass learn from artists working in other media? What lies at the interface of kiln-glass and forms of expression like painting, architecture, photography, digital technologies, printmaking and textiles? Exploring such questions is precisely the goal of the Bullseye Conference, 2011.
WHAT IS BECON?
Every two years, aspiring and accomplished kiln-glass professionals from around the globe enjoy the opportunity to gather, network, compare notes and expand their horizons. That opportunity is known as BECon (the Bullseye Conference).
WHEN IT WILL HAPPEN
June 16-18, 2011.
WHERE IT WILL HAPPEN
Portland, Oregon, USA—on the metropolitan campus of Portland State University, which is central to the city’s vibrant, arts-rich core.
WHO WILL SPEAK
A partial list of presenters includes:
Elizabeth Aro Invorio, Italy
Steve Brown London, England
Bruce Guenther Portland, Oregon, United States
Alex Hirsch Portland, Oregon, United States
Alex Hoare Winchester, England
Munson Hunt Santa Fe, New Mexico, United States
Tom Jacobs Portland, Oregon, United States
Silvia Levenson Lesa, Italy
Dante Marioni Seattle, Washington, United States
Richard Parrish Bozeman, Montana, United States
Marc Petrovic Essex, Connecticut, United States
Laurel Porcari New Orleans, Louisiana, United States
Rick Potestio Portland, Oregon, United States
Judith Schaechter Philadelphia, Pennsylvania, United States
Shapeways Eindhoven, The Netherlands
Karlyn Sutherland Lybster, Scotland
Lino Tagliapietra Venice, Italy
Karen Yair Birmingham, England
WHO WILL ATTEND
About 250 artists, designers, fabricators, instructors, and students from around the globe.
PRE- AND POST-CONFERENCE WORKSHOPS
Are in the planning stages. Update – click HERE to jump to BE workshops.
STUDENT SCHOLARSHIPS
Bullseye is offering 25 scholarships for students. Recipients can attend the conference for $250, less than half the standard price. To qualify, you must currently be enrolled full time in an accredited university or have graduated from an accredited university no earlier than May 2010.
To apply for a scholarship, please email the following information to marketing@bullseyeglass.com by February 13, 2011:
1) your contact information, including name, website (if applicable), mailing address, and email address
2) your CV or résumé
3) a short paragraph describing how you will use what you learn at BECon 2011
4) four to six .jpg files showing your work (no file larger than 100 kb.)
5) a list identifying each work shown in the .jpg files by title of image, title of work, year, technique/media, dimensions, and photographer.
Scholarship recipients will be notified by email no later than February 27, 2011. Once notified, recipients will be able to register for the conference at the reduced rate of $250.
APPLICATIONS
Will open early in 2011.
CONTACT & INFO
Contact conference@bullseyeglass.com for more information.
Click here and here to learn about Portland, Oregon.