Most of you know about the Washington Glass School’s extensive glass classes and the artwork, but many of you don’t know the third component of the Washington Glass Studio. The Washington Glass Studio was established in 2001 to deliver artwork to the public realm by creating site specific art for architectural and landscape environments. Here is a highlight of a few recent projects to give a scope of what we are capable of producing.
We are currently finishing a commissioned public art sculpture in Washington, DC’s Ward 7 – in front of the Unity Parkside Health Clinic and across the street from Caesar Chavez High School. This sculpture will be one of the first public art projects in Ward 7. Consisting of a 16 foot high tri-sided glass covered arch, the entire concept was derived from meeting with the community in the Kenilworth neighborhood.
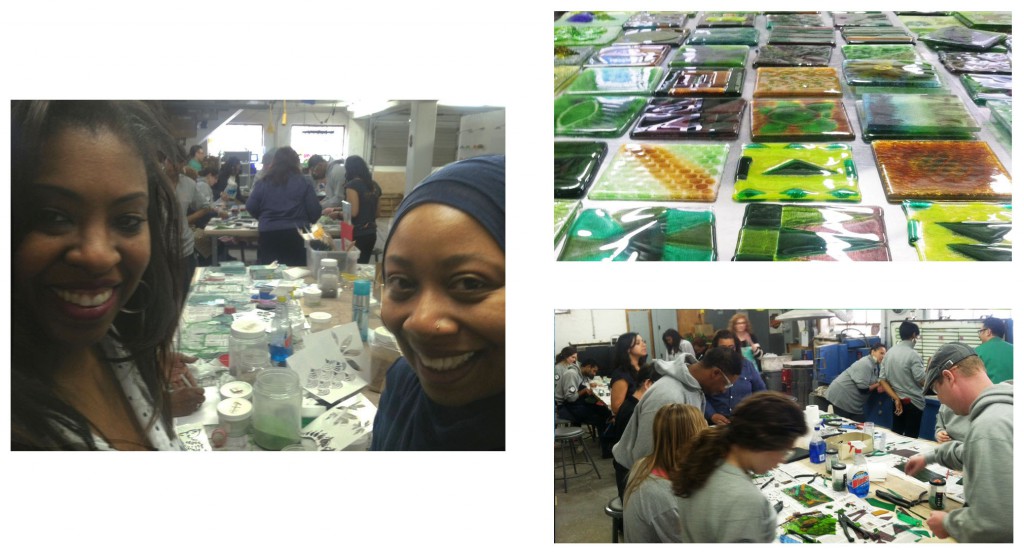
The residents of the community participated in the creation of the glass elements for the public artwork sculpture.
Made up from steel tube sections the steel framework is clad in covered in colorful kilncast glass panels bolted to the structure. Over 300 tiles were required to complete the structure. These 300 tiles we all hand made by volunteers in the community surrounding the arch. The artwork will be internally illuminated with LED lighting throughout the sculpture. Installation is set for end of May/early June.
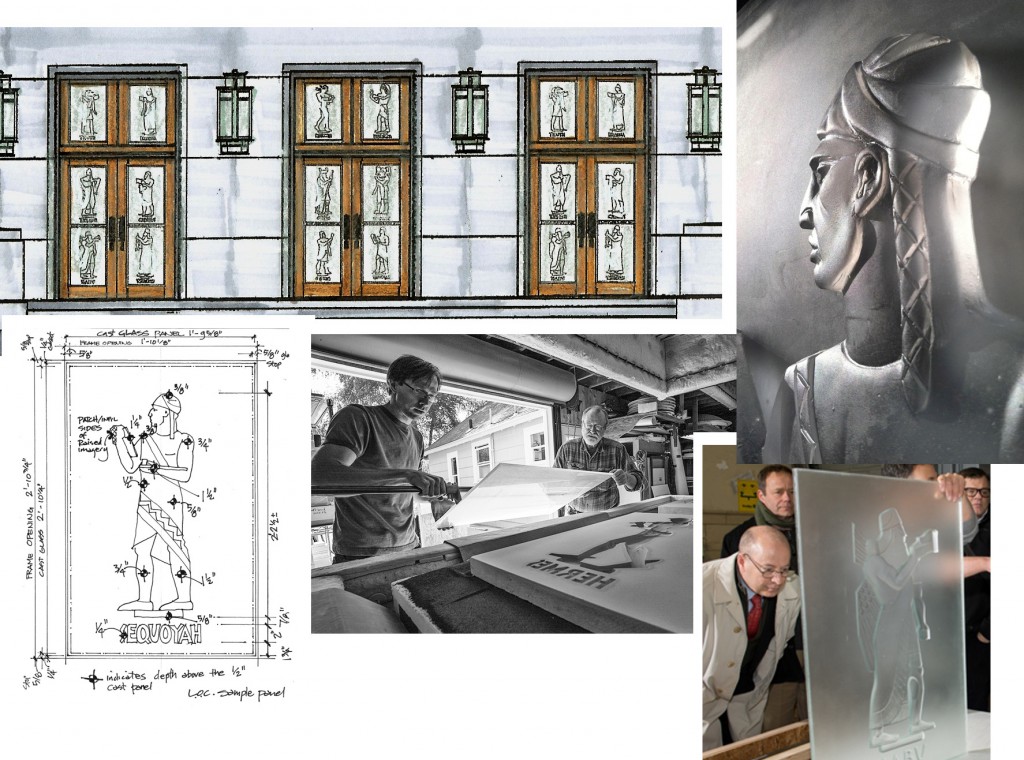
The Architect of the Capitol provides design direction for the historic Library of Congress Adams Building.
Of our recent public art works, the most acclaimed is our cast glass doors for the Library of Congress’ Adams Building. The original doors were cast bronze from the early WPA days. They were designed by Lee Lawrie, who is most known for his designs at Rockefeller Center in NYC. The original bronze bas-relief doors had ceased to be functional years ago, and the entrances were not up to current safety and security code. In a moment of courage and insight, one of the architects of the Architect Of The Capital’s office realized that if the bronze doors were redesigned with glass replicas of the original bronze bas-relief, then he could bring them up to code and increase safety, for much less money. We then took on this multi-year project, with spectacular results.
There were 6 sets of these doors, facing the east and west sides of the Adams Building. American Craft Magazine did a feature story on our work for the Library of Congress and its process – click here to jump to the magazine’s article online.
A smaller scale work was created for the charity organization “Food and Friends” new outdoor park. We made a cast glass Donor Wall that was to honor those who have passed away, to support to charitable work of the organization and to encourage donors to participate. Bas-relief cast glass panels in complementary colors set into a steel framework allows light to pass thru the memorial wall and create colors and patterns on the surrounding plaza. The nature of the glass panels encourages tactile investigation and contemplative interaction.
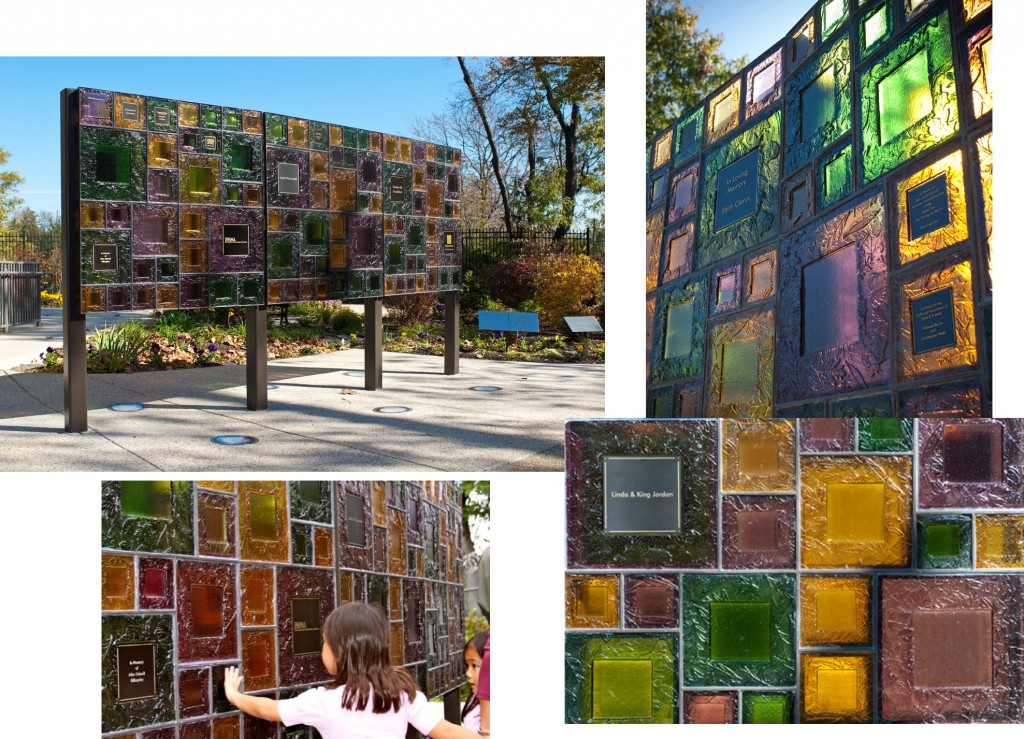
Food and Friends organization commissioned an outdoor donor wall for their park alongside the charity’s Washington, DC facility.
Lastly, one of our most distinguished works was for the Safeway supermarket Bethesda, Maryland. The original store was to be demolished to make way for a much larger structure with parking on the ground floor. As the grocer was committed to Green building, the new structure was to be the first LEED certified grocery store in Montgomery County, and we integrated eco-friendly materials, using recycled glass from the demolished store and re-purposing them to make the new glass and steel ground level building façade. The ground floor building skin was designed to conceal the parking garage function without completely enclosing it. Here is the result:
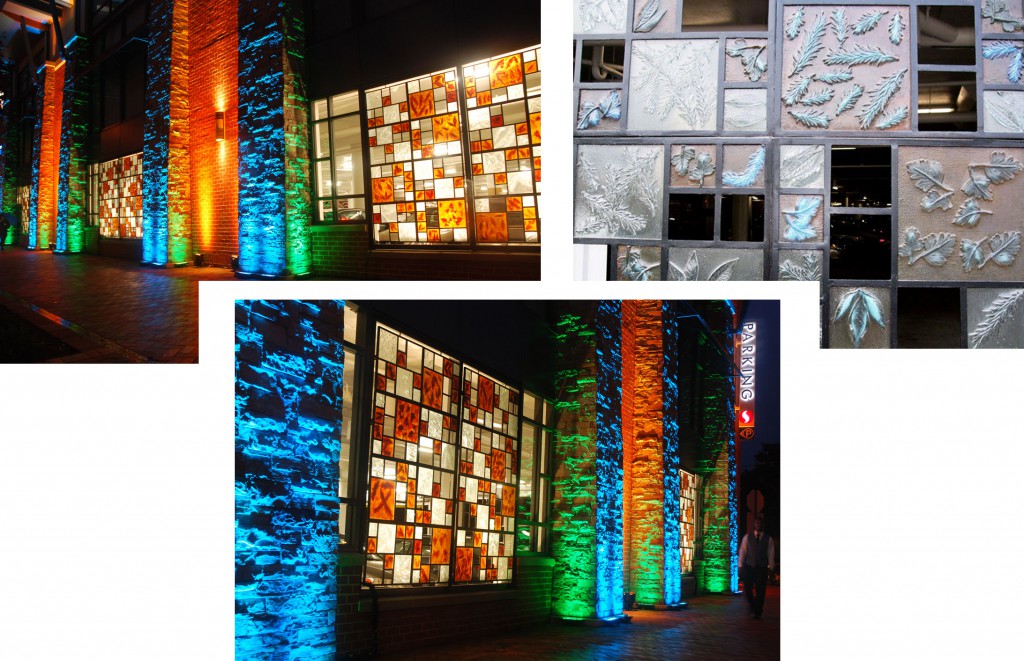
Glass recycled from the original site’s building was incorporated into Safeway supermarket’s first LEED certified building in Montgomery County, MD.
This is only a fraction of what we have competed and what we are capable of doing. No job is too large or too complex. Our architectural design and technical team work well with architects and designers. We are currently looking for additional projects, so let us know in case you know of any, or know someone who might!