With the Memorial Day Weekend here, a blog posting that touches on themes of American Art & history is in order.
 |
Library of Congress, Washington, DC, Adams Building |
The Process looks at how the Washington Glass Studio artists are recreating the original, historic bronze doors from the Library of Congress (LOC) Adams Building in kiln-cast glass.
As mentioned in an earlier post, the Architect of the Capitol (AOC) oversees this landmark building, and they sought out ways to provide up-to-date functional aspects for their structures, all while balancing the requirement for maintaining the artistic legacy of its buildings – a daunting task in an ever changing world. Their design for the LOC Adams building was to have the historic bronze entry doors (that could not be brought up to code) set in the “open” position, and install new code-compliant functional glass doors for the public access – with the glass doors designed to reference the original door sculptures. (Click HERE to jump to link post of sculpted bronze door features.) Washington Glass Studio is creating the new cast glass panels, and this edition of The Process looks at how the molds are being taken from the original doors in-situ.
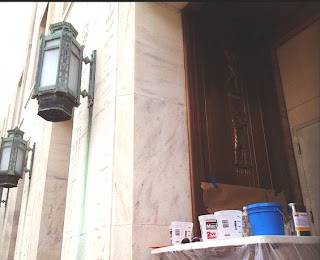 |
Sean Hennessey, the master caster, sets up his mold making equipment and preps the doors. |
The LOC was very concerned that the mold taking process could adversely impact the patina of the bronze doors, so before any work on the doors was completed, testing of the materials and release agents were conducted on an inconspicuous section of the backside of the doors.
 |
A section of the door backside was tested for any reaction to the materials. |
 |
The sample came off with no residue or impact to the original bronze finish. |
 |
Given the go-ahead, Sean enjoys a day in the sun. |
 |
The bronze door area surrounding the bas-relief is masked off. |
 |
Care is taken for the surrounding area. Sean shown here assisted by Erin Cumbo. |
 |
The layering of the silicone rubber mold material starts. |
 |
The mold is allowed to set-up until firm, and then peeled off. |
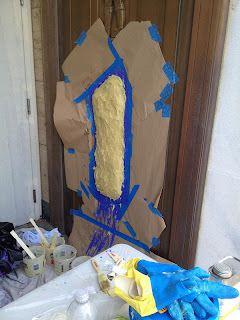 |
“Mother Mold” material is added to give structural strength to the casting. |
 |
The finished rubber mold. |
The molds will later be used to create the original forms for the kiln-casting process – more about the glass casting process in later postings!.