>
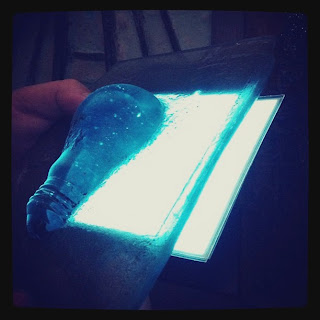 |
Sean Hennessey often incorporates electronics into his cast glass works. Here he is testing new el-wire (electroluminescent) sheet for his panels. |
Artist Sean Hennessey is in da house! (Or at least da Studio!) working on a new series of cast glass/mixed media panels. Fresh from his successful show at Blue Spiral Gallery in Asheville and Artomatic, Sean continues to move forward in his artwork. Sean is kilncasting slabs of glass for his upcoming shows, including “Constructing Content” with fellow Washington Glass artists Erwin Timmers and Erin Antognoli that opens Dec 1 at the Kline Gallery in Frederick, MD’s Delaplaine Arts Center.
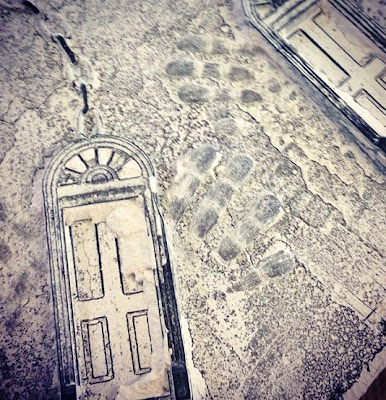 |
Opening the kiln, Sean removes the plaster from cast glass. |
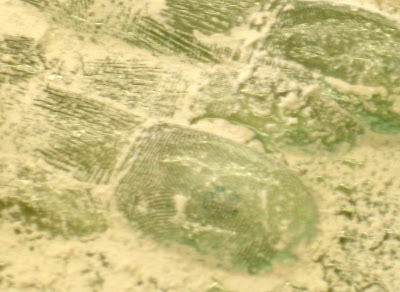 |
Sean’s glass is formed using dry-plaster casting technique captures the detail of his fingerprints. |
Constructing Content
An exhibit featuring Washington Glass School sculptors Erwin Timmers, Sean Hennessey, and Erin Antognoli. The mixed media sculptors combine photography, steel and glass. More will be published online soon!
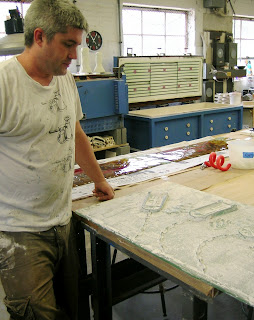 |
Sean appraises the composition of panel after annealing. |
December 1–30, 2012
Kline Gallery
Delaplaine Arts Center
40 South Carroll Street
Frederick, Maryland 21701