>
From this. . . . . . .. . . . . . . .to this.
“It was all her idea”
The History of Pyrex
Back in the early 1900’s, Corning Glass Works was working on a request from the railroads to produce lantern glass that would not break when the hot glass was struck by rain or snow. In response to this request,
In July 1913, a series of events involving Bessie Littleton, the wife of the company’s newest scientist – Dr Jessie Littleton, forced
• The cooking time was shorter
• The cake did not stick to the glass; it was easy to remove with little adhesion
• The cake was unusually uniform
• The flavor of the cake did not remain in the dish after washing
• She could watch the cake bake and know it was done by looking at the underside.
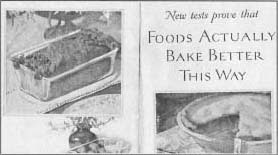
Mr. Littleton brought his wife’s creation to work the following day. Laboratory researchers inspected the cake, which was a “remarkable uniform shade of brown all over.” The men deemed it delicious and very well baked. (A favorite of any lab conclusion, Ed.) Thus began a two-year process to perfect this new invention. The notion of baking in glass was a whole new concept to the public. In 1915, a wondrous new line of “glass dishes for baking” appeared in the nation’s hardware, department and china stores. On May 18, 1915,
The
Click HERE to jump to the story of Harvey Littleton and his historic workshops that brought glass from the factory to the artists.
Other Glass Fun Facts to know and tell:
Glass Fun Facts: Gaffer/Composer
More Glass Fun Facts: Bullseye Glass
Float Glass Fun Facts
Glass Fun Facts – Shattered Glass Predicts Weather
Why is Glass Transparent?
Boro Casting
>
A casting kiln loaded with boro.
Robert Kincheloe has been developing a method of casting using borosilicate glass (aka “hard” glass or 33 C.O.E or Pyrex) and creating components that can later be assembled into Flameworked sculpture.
Rob Kincheloe prepping the glass to be invested into the molds.
Here Rob had made plaster/silica molds via the “lost wax casting” process, and is now loading into the kiln, investing with boro glass.
His process of merging warm and hot glass practices creates one of a kind sculptural works of art.
“Crashing” the kiln to take the glass out of devit range.
The red-hot glass at 2100º F
Some of the cast boro elements – showing the translucent colors. These elements will later be flameworked into sculpture.